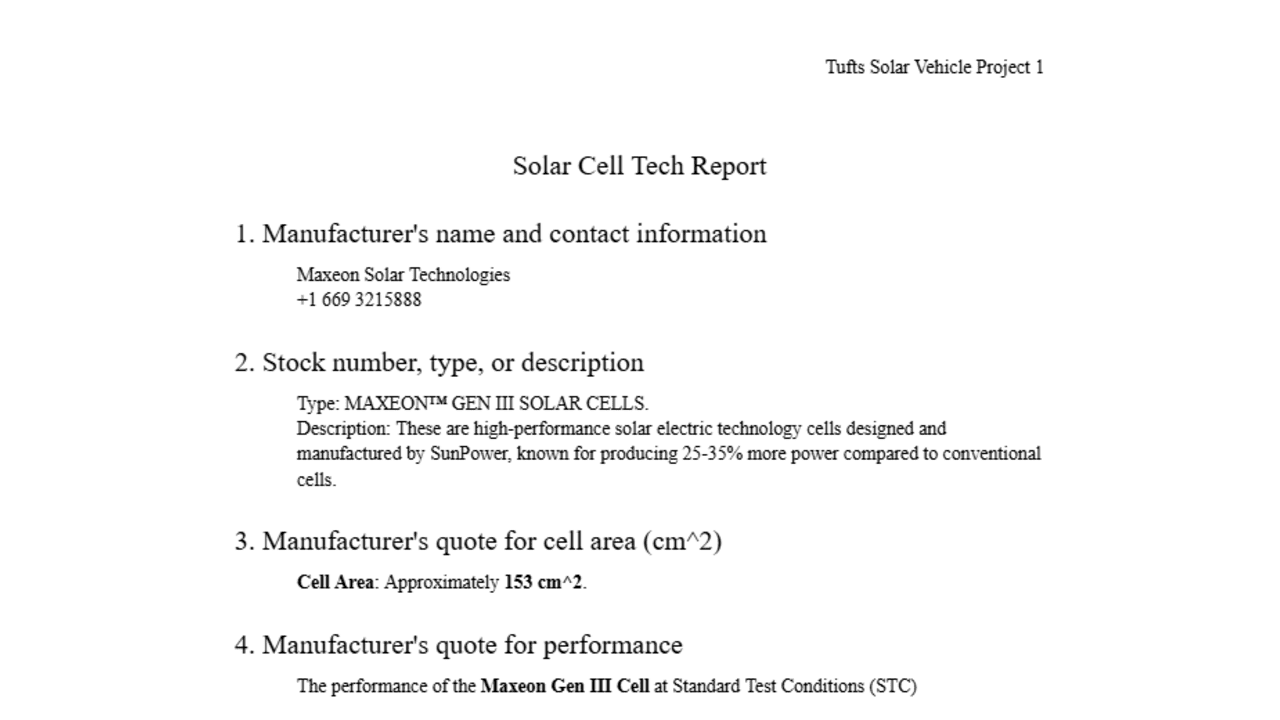
Technical Report
B.S. Electrical Engineering @ Tufts
Skills
Experience
Education
I turn ambition into results. When I moved to Canada at 13, I didn’t speak English and was placed in a 1st-grade English class. During my college applications, I faced rejection from every advising source, but persistence paid off. As a sophomore transfer to engineering, I joined the Tufts Solar Vehicle Project and expanded the team from eight students to a fully functioning operation. By reaching out to professionals, faculty, and peers, I completed the entire solar array manufacturing process in six months, using only 0.5% of the budget typically required by conventional methods.
As President of the Tufts Solar Vehicle Project, I lead a multidisciplinary team of 130+ students from diverse technical backgrounds. By focusing on collaboration and community, I recognize people’s strengths and foster teamwork across the Mechanical, Electrical, and Business teams. Whether it’s through innovating with advanced materials or tackling complex electrical systems, I encourage our team to challenge themselves, continuously learn, and bring diverse perspectives to fuel our success. Together, we are building Tufts' first road-legal, race-competitive solar car, contributing to a more sustainable future.
From developing bioelectrical sensing solutions at Tufts NanoLab using triboelectric nanogenerators to leading the creation of the only MVP greenlit for development at Recruit Holdings, where I managed a cross-functional team and secured executive buy-in after 100+ customer interviews, my focus is on creating products that add value, solve environmental challenges, and are viable for businesses. I bring expertise in agile project management (Scrum, Kanban, sprint planning), Lamination, C, FPGA, VHDL, BOM, and Circuit Design, gained through both coursework and projects.
Impact
Workshops
As co-Electrical Lead of the Tufts Solar Vehicle Project (TSVP), I led a team of 4 to develop a machine that streamlined the production of solar panels, which were essential for powering our solar vehicle. By building our own testing equipment and workspace, we reduced costs by 99.95% and completed the project in just four months. Our team produced high-quality solar panels to maximize the vehicle’s performance, all while staying within a limited budget and spending only an additional $376 beyond sponsored materials.
Technical Report
Electrical System
Lamination Machine
Project Structure
Gantt Chart
Itemized Budget